Weld Types
MIG vs TIG Welding: Which one is best for you?
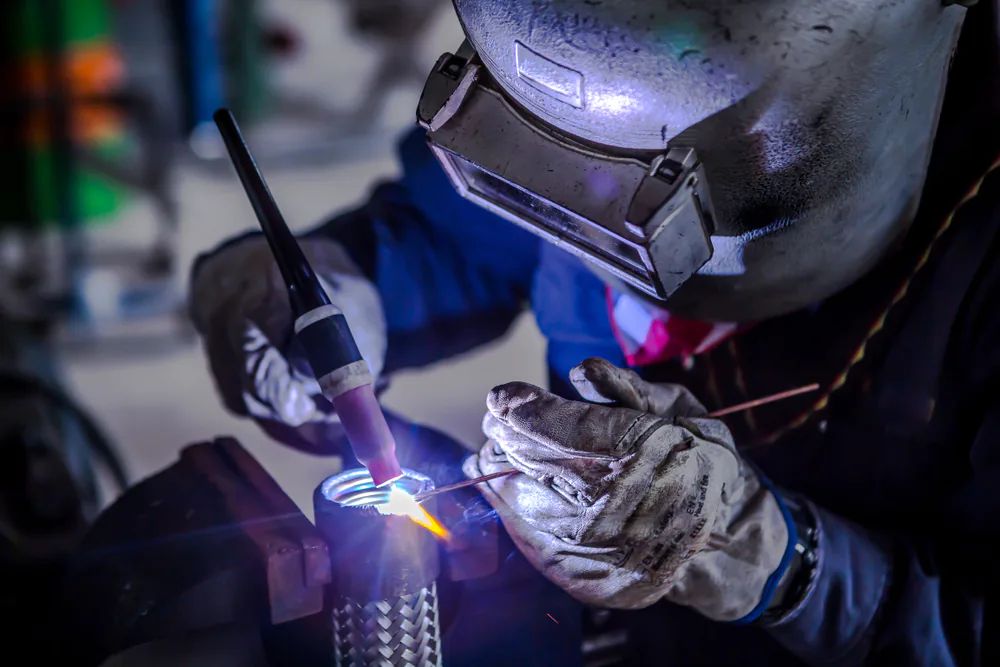
It can be difficult to choose between MIG and TIG welding because you won’t be able to decide which process is best for your material unless you understand the differences between the two. This is exactly what I’m going to determine: whether MIG or TIG welding is better, and what advantages and disadvantages each has.
MIG welding is relatively fast and easy as compared to TIG welding. While the biggest advantage of TIG welding is it’s precision and flexibility that can be achieved with almost any type of metal. With the exception of a few metals with extremely low melting points, TIG welding can weld any metal in an efficient and attractive manner. When compared to MIG welding, TIG is remarkably dynamic.
But those aren’t the only benefits that come with using tig welding. In the following paragraphs, we will discuss the benefits and drawbacks of both processes, as well as how you can select the best method suited to the work you need to do.
MIG vs TIG Welding
Property | MIG Welding | TIG Welding |
Cleanliness | ✅ | ✅ |
Strength | ❌ | ✅ |
Speed | ✅ | ❌ |
Cost Efficient | ❌ | ❌ |
Large Pass Size | ✅ | ❌ |
Position Flexibility | ❌ | ✅ |
Easy to Learn | ✅ | ❌ |
Ease of Maintenance | ❌ | ✅ |
Visibility During Welding | ❌ | ✅ |
Can be Used on Various Thicknesses | ✅ | ✅ |
Small Gun Size | ❌ | ✅ |
Can Perform in Windy Situations | ❌ | ❌ |
Advantages of MIG Welding
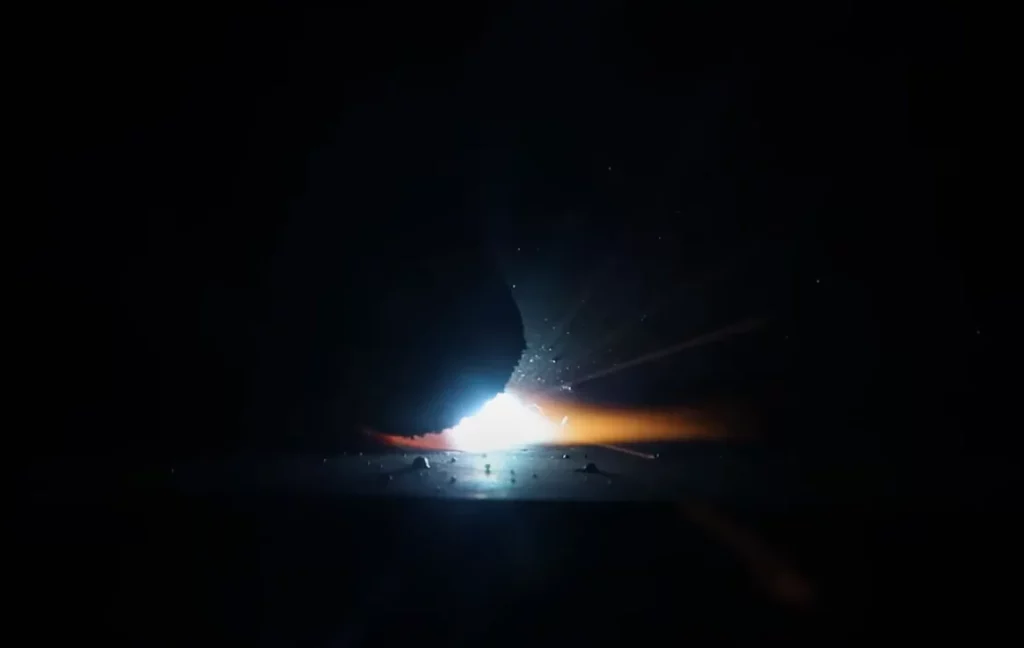
Here are some of the benefits of MIG welding:
- It’s quick.
- It’s Simple
- It gets rid of almost all of the need to clean up.
- It eliminates electrode stub loss
- Uses a wide range of metal thicknesses.
- Allows larger passes to be made with just one weld.
- Lessens the amount of starting and stopping
Let’s discuss these benefits in more depth
1. It’s Fast
This isn’t exactly “another” advantage, but it’s significant enough to mention twice. MIG welding, with its continually supplied electrode, would easily defeat all other major welding processes in a fair fight.
Unlike arc welding, which requires you to provide your own gas/arcs, MIG welding may be done practically continuously from start to finish without the need to change your gas or arc setup at any time. This makes it excellent for joining parts when there isn’t enough time or room to use an electric welder or an oxy-acetylene torch.
2. It’s Simple and Easy
My concept of “simple” does not imply that your ten-year-old kid can learn MIG welding abilities in 15 minutes this weekend. Welding and children should never be mixed in any manner, just as weight lifting and roller skating should never be done concurrently.
Because many of the operations that occur during MIG welding are automated, MIG welding is significantly simpler to learn and much faster to master than other methods of welding, such as tig welding. The constantly supplied electrode is at the very top of this list.
3. Almost Zero Cleanup
It eradicates the requirement for hardly any time spent cleaning up. Mig welding isn’t nearly as clean as tig welding, but when compared to stick welding, it’s still a significant improvement in terms of cleanliness.
Due to the fact that MIG welding generates extremely little slag, there is no longer a need to clean the weld joint after each and everyone (debris). Because there is no flux present during MIG welding, there will be no accumulation on the surface of the component that is being welded. This is another advantage of MIG welding.
4. No Electrode Stub Loss
One thing that irritates me about stick welding is that no matter how well I weld, I can’t use the last few inches of an electrode. Stick welding is dangerous, inefficient, and nearly impossible to use the entire electrode.
But when MIG welding, you can use the whole electrode. It enables you to make use of the entire length of your electrode. This means that when using stick welding, you don’t have to worry about being wasteful because you can use the entire length of the electrode.
5. Works With a Wide Range of Metal Thicknesses
Mig welding almost works on all types of metal, with differing thicknesses. Mig welding produces smooth, strong weld beads with good penetration. The penetration of a weld depends on the current used, but it also depends on the type of material being welded. In general, thicker metals require a higher current to produce a good bead; thin materials require less current to produce a good bead.
6. Large Passes with One Weld
The width of the MIG weld pool is directly proportional to the speed of travel, or how rapidly the welder is working. As a consequence of this, it is possible to link considerably larger parts in a single pass.
One of the reasons why MIG welding is faster than other techniques is because it takes longer passes. Due to the fact that MIG welding runs deposit more metal with each pass, bigger joints need a lower total number of passes.
7. Less Amount of Starts and Stops
One other advantage is that it reduces start-and-stops. A constantly supplied electrode reduces the number of times you have to stop welding, modify or fetch a new electrode, and start again.
This may not seem like much, but think of how much time you may waste stopping and beginning throughout the life of a project.
It also helps with material selection. When we want to use thicker gauge metals for our projects, it becomes harder to find high-quality tungsten electrodes in smaller gauges than we need for our welds. MIG welding allows us to use these thinner gauges without having to worry about damaging our tungsten electrodes by trying to fit them into a larger gauge machine.
Limitations of MIG Welding
Here are a few of the limitations/disadvantages of MIG welding:
- Costly equipment
- Equipment requires more maintenance
- Difficult or perform in an open area
- Welding guns are bigger and heavier
So let’s discuss these key limitations one by one:
1. MIG Welding Requires Costly Equipment
Equipment used for MIG welding is typically more expensive than equipment used for stick welding. This is especially the case when one considers the cost of stick welding equipment in contrast to the cost of MIG welding equipment. Stick welding equipment is simpler and less expensive than MIG equipment, especially the machine itself.
2. MIG Equipment Requires More Maintenance
Unfortunately, repairing or cleaning steel-reinforced MIG welding equipment requires a lot of time off from work. If you do not have a backup for your equipment then It’s not uncommon for a shop to have to shut down for several days because of downtime caused by this problem.
That’s why it’s important to know what maintenance your MIG welding equipment needs on a regular basis so that you can get the most out of it and keep it running smoothly.
3. Outdoor MIG Welding is Quite Challenging
Mig welding equipment is useful for a variety of applications, but it can be difficult to ensure that you’re getting the most out of your equipment when working outside.
It’s not just the wind; even a light breeze will make it difficult to complete your tasks. It can also be difficult to move around if you’re using large or heavy machinery. When it comes to large machines, there are also safety concerns about where they go and how they get in and out of the shop.
4. Big Gun is Being Used
Mig welding guns are quite large. Because there is so much going on inside a MIG welding gun, it is likely to be a larger piece of equipment than what you are used to using for stick welding.
For example, working in a confined space can make it difficult to properly manipulate a MIG welding gun. As a result, it is critical to determine whether the space will allow you to move around the welding gun without colliding with it while performing the task.
Advantages of TIG Welding
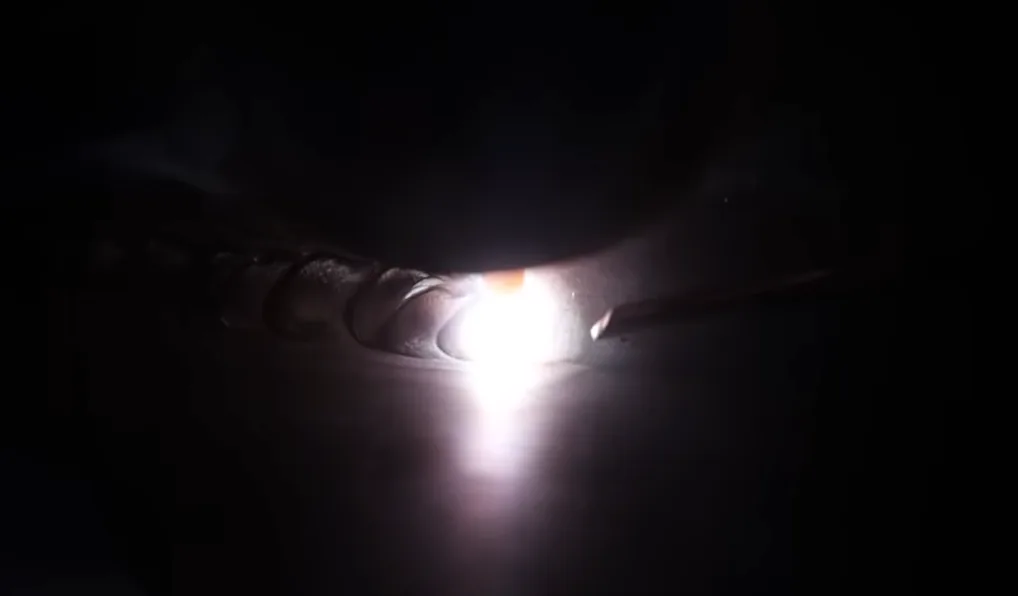
Here are some of the benefits of TIG welding:
- Can be used in almost any position
- Requires very little finishing
- Ductile and stronger joints
- It is an extremely clean process
- It has Very high visibility
- Can be used on many different thicknesses
So let’s discuss these advantages in detail:
1. Position Freedom
Due to the very small gun and machine, it can be used in almost any position. You don’t need to worry about tight corners anymore.
2. Very Little Finish Required
When using tig welding, relatively little finishing is required. Stick welding normally requires the use of a chipping hammer and a wire brush to remove slag, but when you are MIG welding, you do not waste your time in this manner.
3. Ducticle, Stronger and More Resistant to Corrosion
When compared to the joints that are created using other methods of welding, the joints that are produced by this method are more ductile, stronger, and resistant to corrosion.
Joints that are ductile are less prone to shatter since they are not as brittle.
4. Very Clean Process
The tig welding procedure is very environmentally friendly. The byproducts of tig welding are significantly less splatter, smoke, sparks, and fumes, as well as a lot less mess than what was previously available when using several alternative welding techniques.
Even though tig welding generates far less smoke and fumes than stick welding does, enough ventilation is still required, and this is particularly important when tig welding copper alloys. When you tig weld copper alloys, very poisonous vapors are produced as a byproduct of the process.
5. Gives You High Visibility While Welding
The sight that you have when tig welding is unparalleled or at least unparalleled to any other welding method. When compared to stick welding, tig welding generates very little smoke and makes use of colorless shielding gases. As a result, you are able to see your work more clearly when tig welding than you would be able to on a similar stick welding operation.
6. Can be Used on Many Different Thickness Metals
There are many different materials that may be welded using the TIG welding technique since it is such a flexible method of welding. With TIG welding, it is possible to weld metals of a broad range of thicknesses, and this includes very thin materials, which may be very challenging to weld using traditional welding procedures, or maybe even impossible to weld.
Amperage settings for TIG welding may vary from as little as 5 amps to as high as 800 amps. This gives the welder a great deal of flexibility while working with the process.
Limitations of TIG Welding Comparison
If you have just finished reading such a lengthy list of the advantages of tig welding, you might be tempted to simply give in to your feelings and dedicate yourself to TIG welding with your whole heart. Just a second, please!
TIG welding, just like any other type of welding technique, has a few limitations, some of which are more apparent than others. The most significant disadvantages of tig welding are mentioned below:
- It is a very slow process
- It’s difficult to learn
- Can be difficult to perform outside
- Expensive equipment
1. TIG Welding is Slow
TIG welding is a slow method. Even after you’ve mastered the skill, the pace is slow compared to other types of welding.
2. You can’t learn it in Just One Night
It takes time to become proficient at TIG welding. Because it is such a difficult procedure, the majority of people require extensive training before they can achieve any significant level of success.
3. Quite Challenging to Perform Outside
Tig welding must be performed in an environment that is constant and regulated, such as a welding shop; it is difficult to do in any other environment. Because of this, TIG welding in the open air, especially in situations when there is a lot of wind, may be challenging.
4. Requires Expensive Equipment
The supplies and equipment needed for TIG welding are both quite pricey. Stick welding requires a significantly lower initial investment than tig welding does, but tig welding does require a significantly higher initial investment than stick welding does.
Related Questions
1. MIG vs TIG Welding Strength?
TIG welding produces more strong, ductile, and corrosion-resistant joints as compared to MIG welding.
2. MIG vs TIG Welding Speed?
MIG welding is a more fast and more speedy process as compared to TIG welding. The main reason for this is that MIG welding uses a wire that has a high current density, which causes the metal to melt as soon as it comes in contact with the electrode. This makes the process of MIG welding very efficient and faster than TIG welding.
Summarizing the Results
It is essential to consider the sort of joint that you want to weld before making any decisions. Every method has certain benefits and drawbacks exclusive to itself. MIG welding is the most efficient method if you are interested in working quickly. TIG welding, on the other hand, is the method to use if you want a greater degree of flexibility and accuracy in your work.
Weld Types
Different Welding Methods: Applications of Each Method
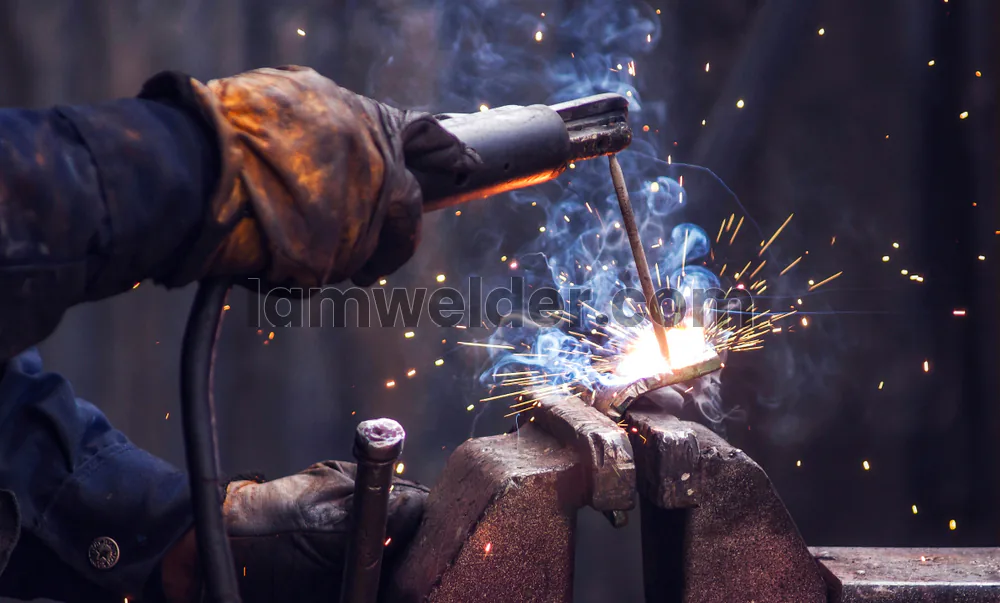
Welding is joining two pieces of metal together by melting and cooling them until they become one piece. Welding processes include:
- Oxyacetylene welding
- Shielded metal arc welding (Stick)
- Gas tungsten arc welding (TIG)
- Gas metal arc welding (MIG)
- Flux-cored arc welding
- Torch or oxyfuel brazing
Some methods employ both heat and pressure, while others employ only heat. Welding is commonly used to construct automobiles, airplanes, and buildings. Other metal-cutting methods, such as oxy-acetylene and plasma arc cutting, use heat or electricity to cut through metal.
1. Oxyacetylene welding
Oxyacetylene welding (OAW) is a method of joining two pieces of metal using heat generated by the combustion of oxygen and acetylene gas.
Torch brazing (TB) is similar, but the metal is not completely melted. Instead, a special alloy is melted and used to join the two metal pieces.
Oxyfuel gas cutting (OFC) is a method of cutting metal that uses the same tools and gases as OAW and TB.
To generate heat and bond the metal, all of these methods employ a torch and special gases. They are frequently used on small or thin metal pieces.
Applications:
- Welding and brazing thin or small pieces of metal
- Welding and brazing dissimilar metals
- Cutting and piercing metal
Situations to Avoid:
- Welding thick or heavy sections of metal
- Welding high alloy or stainless steel
- Welding in high wind or outdoor conditions (due to the open flame)
- Welding in confined spaces (due to the production of harmful gases)
2. Shielded metal arc welding (Stick)
Shielded metal arc welding, or SMAW, is a way of welding metal together using an electrode that is coated with a special kind of flux.
The electrode melts and becomes a part of the welded metal. To do SMAW welding, you need a transformer, two welding cables, a work clamp, and an electrode holder.
There are many different types of electrodes you can use for SMAW welding, so you can choose the one that is best for your project. With SMAW welding, you can join different types and thicknesses of metal using the same machine.
Applications:
- Welding thick or heavy sections of metal
- Welding in outdoor conditions
- Welding in dirty or contaminated environments
- Welding on dirty or painted surfaces
Situations to Avoid:
- Welding thin or small pieces of metal (more suited for TIG welding)
- Welding high alloy or stainless steel (can affect the quality of the weld)
- Welding in confined spaces (due to the production of harmful gases)
- Welding in the presence of high winds (due to the electric arc)
3. Gas tungsten arc welding
GTAW, or gas tungsten arc welding, is a method of joining metal using a tungsten electrode. The tungsten electrode generates an electric arc, which melts the metal being welded as well as the end of the filler metal, which is manually applied.
Shielding gas is emitted from the welding gun to protect the molten weld metal from dirt and other contaminants. A foot or thumb switch can be added to the GTAW equipment to help the welder better control the welding.
GTAW welding produces very clean, high-quality welds, but it is slower and requires more skill than other welding methods. It is particularly useful for joining metal alloys that can only be joined with GTAW.
Applications:
- Welding thin or small pieces of metal
- Welding high alloy or stainless steel
- Welding in outdoor conditions (with proper shielding gas)
- Welding materials with high levels of contaminants or impurities
- Welding in high-precision environments
Situations to Avoid:
- Welding thick or heavy sections of metal (more suited for MIG welding)
- Welding in high production environments (slower process)
- Welding in confined spaces (due to the production of harmful gases)
- Welding in the presence of high winds (due to the electric arc)
4. Gas metal arc welding (MIG)
Mig welding is a type of arc welding that uses a continuously supplied wire electrode and gas to weld metal together.
It is becoming more popular because it is easier to learn than other types of welding, like stick and tig welding, and it is faster because you don’t have to stop and change the electrode as often.
Mig welding also creates less slag and spatter, which makes it more enjoyable to use and easier to clean up.
However, MIG welding equipment is more expensive and the MIG gun, which is the portable part of the equipment, can be difficult to use in small spaces. Mig welding also requires a shielding gas to work, so it is not as good for outdoor use.
Applications:
- Welding thick or heavy sections of metal
- Welding high alloy or stainless steel
- Welding in high-production environments
- Welding in outdoor conditions (with proper shielding gas)
Situations to Avoid:
- Welding thin or small pieces of metal (more suited for TIG welding)
- Welding in confined spaces (due to the production of harmful gases)
- Welding in the presence of high winds (due to the electric arc)
- Welding materials with high levels of contaminants or impurities (can affect the quality of the weld)
5. Flux-cored arc welding
Flux-cored arc welding, or FCAW, is a method of joining metal using a special type of electrode wire known as a flux core wire.
The wire is fed from a spool continuously through the welding equipment and out of the gun. The welding current flows through the equipment, melting the wire and the base metal.
Some flux core wires generate their own shielding gas as they melt, while others require the use of additional shielding gas. As the wire melts, it produces a gaseous cloud that shields the weld surface and removes impurities from the molten metal.
After the weld is completed, a layer of slag must be removed from the weld’s top. Despite this additional step, FCAW is a popular welding technique because it produces high-quality welds quickly and is very versatile.
FCAW equipment is similar to that used in gas metal arc welding (GMAW), and both methods are semiautomatic, which means that the wire is fed automatically but the welder moves the gun manually. Welding supply stores and other retailers stock FCAW equipment and filler metals.
Applications:
- Welding thick or heavy sections of metal
- Welding in outdoor conditions (with proper shielding gas)
- Welding in high-production environments
- Welding in dirty or contaminated environments
Situations to Avoid:
- Welding thin or small pieces of metal (more suited for TIG welding)
- Welding high alloy or stainless steel (can affect the quality of the weld)
- Welding in confined spaces (due to the production of harmful gases)
- Welding in the presence of high winds (due to the electric arc)
Comparison Table:
Welding Process | Applications | Situations to Avoid |
---|---|---|
Oxyacetylene welding | Welding and brazing thin or small pieces of metal; welding and brazing dissimilar metals; cutting and piercing metal | Welding thick or heavy sections of metal; welding high alloy or stainless steel; welding in high wind or outdoor conditions; welding in confined spaces |
Shielded metal arc welding (Stick) | Welding thick or heavy sections of metal; welding in outdoor conditions; welding in dirty or contaminated environments; welding on dirty or painted surfaces | Welding thin or small pieces of metal; welding high alloy or stainless steel; welding in confined spaces; welding in the presence of high winds |
Gas tungsten arc welding (TIG) | Welding thin or small pieces of metal; welding high alloy or stainless steel; welding in outdoor conditions (with proper shielding gas); welding materials with high levels of contaminants or impurities; welding in high-precision environments | Welding thick or heavy sections of metal; welding in high production environments; welding in confined spaces; welding in the presence of high winds |
Gas metal arc welding (MIG) | Welding thick or heavy sections of metal; welding in high production environments; welding in outdoor conditions; welding on dirty or painted surfaces | Welding thin or small pieces of metal; welding high alloy or stainless steel; welding in confined spaces; welding in the presence of high winds |
Flux-cored arc welding | Welding thick or heavy sections of metal; welding in high production environments; welding in outdoor conditions; welding on dirty or painted surfaces | Welding thin or small pieces of metal; welding high alloy or stainless steel; welding in confined spaces; welding in the presence of high winds |
Informational
Selecting the Best Gas for MIG Welding [Downloadable Chart]
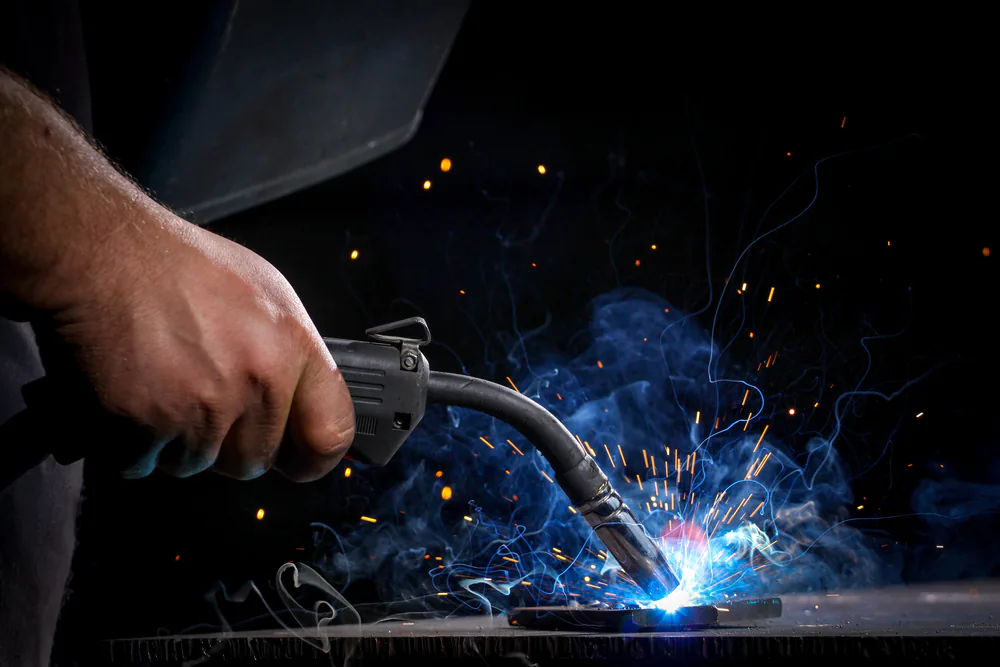
There is a direct correlation between the type of weld that is produced and the shielding gas that was used during the welding process. The manner in which the metal is distributed, the welding speed, the weld contour, the effect that the arc has on cleaning, and the fluidity of the molten weld pool are some of the properties that may be affected.
So, in this article, we will go over all of the different types of gases that can be used in MIG welding to improve weld quality.
The five most common gases used in MIG welding are Argon, Carbon Dioxide Helium, Oxygen, and Nitrogen. Each gas has its own benefits and problems. But Argon and Its mixes are the most widely used gases for MIG welding.
Choosing the Right Gas Type for Your Job is Not Simple, You Need More Information
As I mentioned earlier, Shielding gas is essential for MIG welding because it prevents the weld puddle from becoming contaminated by the atmosphere. It is critical that the shielding gas moves over the work area at a nice and consistent rate.
The shielding gas supply configuration in a MIG welding operation is relatively simple. The gas is contained in a pressurized cylinder, and a flow meter is used to reduce the pressure of the gas to a workable level.
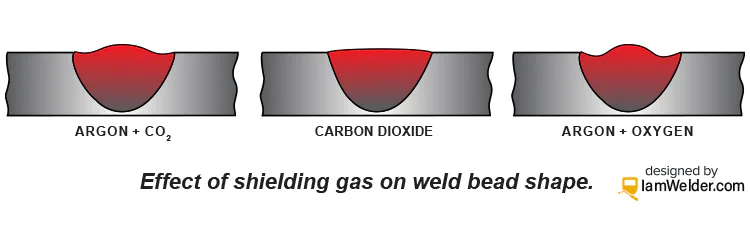
The gas is then piped into the MIG welding gun and directed onto the molten pool via a nozzle. But the choice of which shielding gas to use for your MIG welding projects is not an easy one.
When deciding which shielding gas to use, there are several options to consider, as well as several criteria to consider. These criteria include the depth of penetration, porosity prevention, welding speed, and, of course, cost.
In the following paragraphs, I’ll give you some additional information to help you decide which approach to your MIG jobs will be the most successful.
Most Widely Used Gases for MIG Welding
There are five most widely used gas types in MIG welding:
- Argon (Ar)
- Carbon Dioxide (CO2)
- Helium (He)
- Oxygen (O)
- Nitrogen (N)
[table id= 19/]
[table id= 20/]
1. MIG Welding With Argon
The atomic symbol for argon is Ar, and it is categorized as an inert gas. Inert gases are those that do not react with other substances and are also insoluble in molten metal.
While welding nonferrous metals such as aluminum, copper, magnesium, and nickel, as well as their alloys, you can use argon at a concentration of one hundred percent; however, pure Argon is not commonly used when welding ferrous metals.
Due to the fact that argon is heavier than air (unlike helium; we will discuss this in more detail in the following paragraphs), you require less of it when welding because it flows directly onto the weld area from the nozzle. This is one of the most significant advantages of argon.
On the other hand, Argon ionization is not very difficult. Gases that ionize quickly may support longer arcs at lower voltages than other kinds of gases. As a result, it is less susceptible to fluctuations in arc length.
Argon or a combination of argon with other gases is good for the axial spray transfer procedure. Helium and/or oxygen are often combined with argon gas for steel welding.
Argon is an excellent choice if you desire a quiet arc with minimal spatter. You should allocate approximately $100 for a large cylinder of argon or argon mixture.
Pros & Cons of Using Argon Gas in MIG Welding
2. MIG Welding With Carbon Dioxide
One carbon (C) and two oxygen (O2) atoms combine to form carbon dioxide, which has the molecular formula CO2. For MIG welding of steels, carbon dioxide at 100% concentration is commonly used as a shielding gas.
In comparison to inert gases, it allows for faster welding speeds, deeper penetration, superior mechanical properties, and a lower price tag. Carbon dioxide has less steady arc characteristics and significantly more weld spatter, which is the main drawback.
The amount of spatter produced can be minimized by keeping the arc length constant and very short. CO2 can create solid welds if a filler wire with the right deoxidizing additives is used.
In comparison to other gases, its low cost (around $12 for a 244-cubic-foot cylinder) makes it a competitive choice.
Pros & Cons of Using Carbon Dioxide Gas in MIG Welding
3. MIG Welding With Helium
Helium, a nonreactive gas with the atomic symbol He, does not react with molten metals either. Helium can help you make wider welds when welding thick pieces of metal, which is very beneficial in some cases.
The main disadvantage is that because helium is lighter than air, it tends to float away from the weld puddle. And typically necessitates a higher flow rate and significantly more gas than would be required when working with, say, argon.
Because helium is less dense than air, its flow rates must be roughly double those of argon to produce enough gas stream stiffness to displace air from the weld area.
When welding in moist conditions, high flow rates are required to provide adequate protection resulting in high gas consumption.
Higher voltage ionization is required, resulting in a hotter arc. When helium is used, the heat generated by the arc significantly increases. This hotter arc makes welding thick sections of aluminum and magnesium easier.
Helium is added in small amounts to heavier gases. These blends take advantage of helium’s high melting point and the other gas’s superior weld coverage. This means that the blended gas benefits from the properties of both gases.
Helium can consist of up to 80% of a helium/argon mix. If you want more power in your arc without losing the spray mode’s other advantages, mix helium with your argon.
As the amount of helium increases, the transfer becomes increasingly globular, which may require you to change the welding technique. Helium costs approximately $10 more per cylinder (244 cubic feet) than argon.
Pros & Cons of Using Helium Gas in MIG Welding
4. MIG Welding With Oxygen
Although pure oxygen is almost never used in MIG welding but oxygen is very helping in gas mixes. It is really good for stabilizing Arc and minimizing the spatter.
Pros & Cons of Using Oxygen Gas in MIG Welding
5. MIG Welding With Nitrogen
Nitrogen is represented by the atomic symbol N. It’s not an absolutely nonreactive gas, but it won’t cause much trouble in the molten weld pool. It is frequently added to blending gases in order to raise the arc’s temperature. Copper and copper alloys can be welded using pure nitrogen.
Pros & Cons of Using Nitrogen Gas in MIG Welding
Best Mixture Gases for MIG Welding
The welding properties of argon may be altered by combining it with oxygen, carbon dioxide, helium, or nitrogen.
By adding reactive gases (oxidizing) to argon, such as oxygen or carbon dioxide, the arc may be stabilized, metal transfer enhanced, and spatter minimized.
As a result, the penetration pattern is improved, and undercutting is eliminated or reduced.
By introducing inert gases such as helium or nitrogen, the arc heat may be enhanced.
To accomplish the desired results, a very minimal concentration of reactive gases such as oxygen or carbon dioxide is required. A change in oxygen level as minor as 0.5% will have a visible effect on the weld.
Blends containing between 1 and 5 percent oxygen are the most common. Two-thirds of the argon volume can be filled with carbon dioxide.
There may not be enough arc voltage in argon + carbon dioxide +oxygen mixtures with less than 10% carbon dioxide to achieve the desired results. Most applications call for a 25% CO2 argon blend.
[table id= 21/]
Filler wire containing deoxidizers should be used when welding with oxidizing shielding gases like oxygen or carbon dioxide to prevent porosity in the weld.
Some alloying elements, like chromium, vanadium, aluminum, titanium, manganese, and silicon, can be lost due to the presence of oxygen in the shielding gas.
100% argon’s cathodic cleaning action corrodes steels. The arc might be drawn to the iron oxide in and on the steel’s surface because it is a good emitter of electrons.
However, because of the uneven distribution of these oxides, arc movement and weld deposits are highly irregular. The issue was resolved by mixing in some oxygen with the argon.
A uniform film of iron oxide is formed by the reaction, which provides a stable site for the arc and strengthens the weld pool.
Thanks to this breakthrough, GMAW can now be used to weld ferrous alloys, greatly increasing its versatility.
Steel alloys have different oxygen requirements for arc stabilization. In most cases, 2% is adequate for carbon and low-alloy steels.
About 0.5% should be sufficient to prevent a refractory scale of chromium oxide in stainless steel.
CO2 is a viable oxygen replacement. However, more than 2% is required, with 8% appearing to be optimal for low-alloy steels.
Carbon dioxide is often used as an additive because it improves the weld bead’s contour and gives the arc a more stable appearance.
[table id= 22/]
Helium is added to heavier gases in trace amounts. These mixtures capitalize on the helium’s high melting point and the other gas’s superior weld coverage.
This means that the blended gas reaps the benefits of both gases.
Sometimes helium makes up as much as 80% of a helium/argon mix.
If you want more power in your arc without losing the spray mode’s other benefits, mixing helium with your argon is the way to go.
As the amount of helium increases, the transfer becomes increasingly globular, necessitating a switch to a different type of welding (to be described later).
Gases like helium and argon do not react chemically with any metals because they are inert.
Selecting the Gas Type Depends on 3 Factors
When selecting a Gas for your MIG welding projects, there are 3 things that you need to consider before choosing the gas:
- Metal Type
- Metal Thickness
- Wire Size
1. Selecting the Gas Type According to Metal Type
2. Selecting the Gas Type According to Metal Thickness
[table id= 23/]
3. Selecting the Gas Type According to Wire Size
[table id= 24/]
MIG Welding Gas Price Comparison
[table id= 25/]
Final Words
It is recommended that you get in touch with the gas provider in your area prior to making the purchase of a tank.
Although the vast majority of businesses do refill tanks belonging to third parties, the processes that they use to do so can vary. However, before you buy a tank, you should confirm that they will fill it for you.